ARbowhunter7
Opulence...I Has It.
I recently got my truck back from the shop with a mint, fresh head installed. Everything looked fine, but it kept leaking coolant from the heater core outlet at the front of the head. Through all the efforts at tightening/sealing it there's now a hairline crack at the outlet that extends about 1/2" down the front of the head. Not bad, but enough to spray a little coolant.
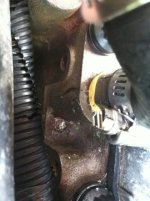
I need to fix it, but I'm a newb when it comes to Devcon repair. Which Devcon would work best here and what's the method of application in a crack that small? How would you prep the surface inside that little crack? And should I remove the fitting before repairing?
Thanks in advance.
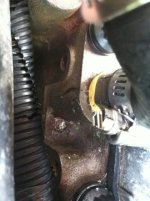
I need to fix it, but I'm a newb when it comes to Devcon repair. Which Devcon would work best here and what's the method of application in a crack that small? How would you prep the surface inside that little crack? And should I remove the fitting before repairing?
Thanks in advance.