BC847
New member
Still poking at it . . .
Lapped the valves today. The machinist was pretty-good with keeping the proper width seat, centered on the valve and what he had to work with in the head (the innermost angle (15*?) is scant in places). If I'm reading the Cummins manual right, this would have been the last time theses valve-seats can be cut (at 0.060" max valve top to head-deck). Service/replacement seats are out of the question as there's been notable whittling in there and to try and blend it in, would leave little on the bottom of the thing.
Started cleaning up the 12mm A1 head-studs harvested from the original build. Still gotta check the lengths.
Lapped the valves today. The machinist was pretty-good with keeping the proper width seat, centered on the valve and what he had to work with in the head (the innermost angle (15*?) is scant in places). If I'm reading the Cummins manual right, this would have been the last time theses valve-seats can be cut (at 0.060" max valve top to head-deck). Service/replacement seats are out of the question as there's been notable whittling in there and to try and blend it in, would leave little on the bottom of the thing.
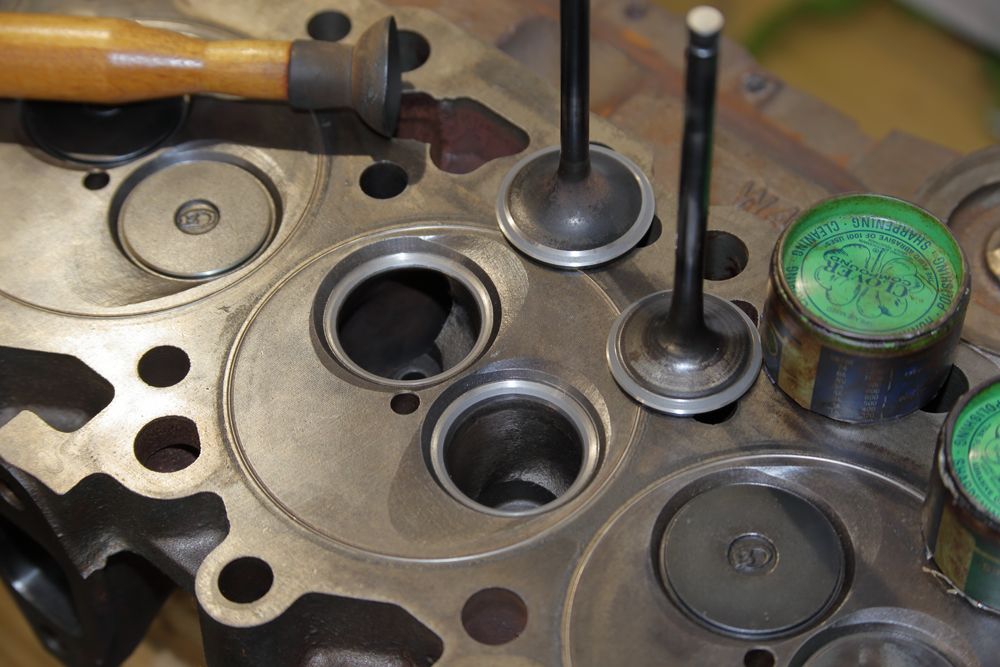
Started cleaning up the 12mm A1 head-studs harvested from the original build. Still gotta check the lengths.
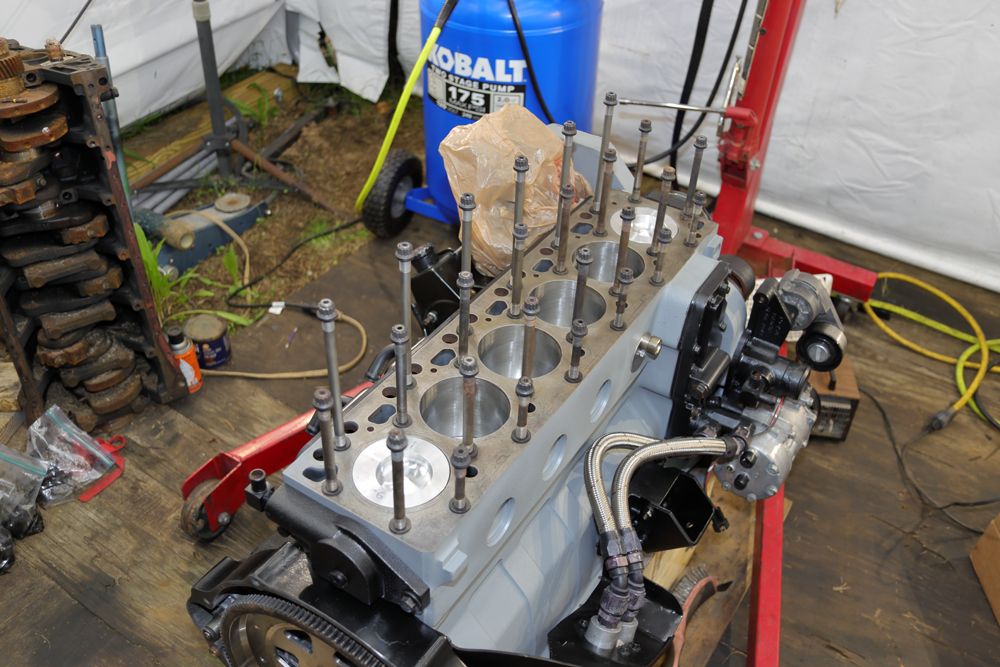