Tacoclaw
New member
Hey, everyone, I've been messing around for about a month trying to get a blower drive pulley made for my truck. I had the equipment to make it, just not the balls, and after getting no calls back after that much time I just went for it. It's all done but the grooves, I've failed three times at grinding an acceptable HSS cutter so I'm having them done by a pro. Even I know my limits, especially when it's the last step.
Once finished I'll turn some more weight off of it and drill some lightening holes in it.
*Disclaimer*
Your results may vary, the measurements are for my '90 W250 with electric fans and a stock balancer. It is unknown if you can run the mechanical fan with this as I have none. My idler mount is #3911660 and the center hole is a slip fit over the fan threads. If you opened it up to clear the hex of the fan it may work.
Once finished I'll turn some more weight off of it and drill some lightening holes in it.
*Disclaimer*
Your results may vary, the measurements are for my '90 W250 with electric fans and a stock balancer. It is unknown if you can run the mechanical fan with this as I have none. My idler mount is #3911660 and the center hole is a slip fit over the fan threads. If you opened it up to clear the hex of the fan it may work.
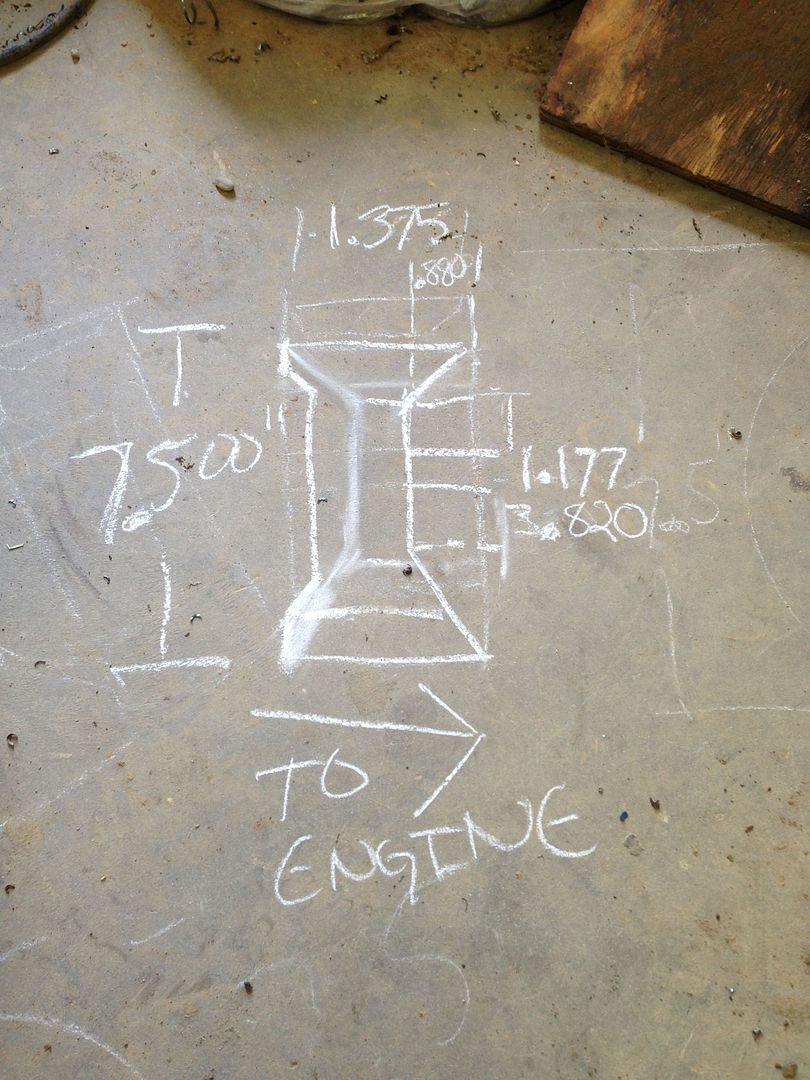
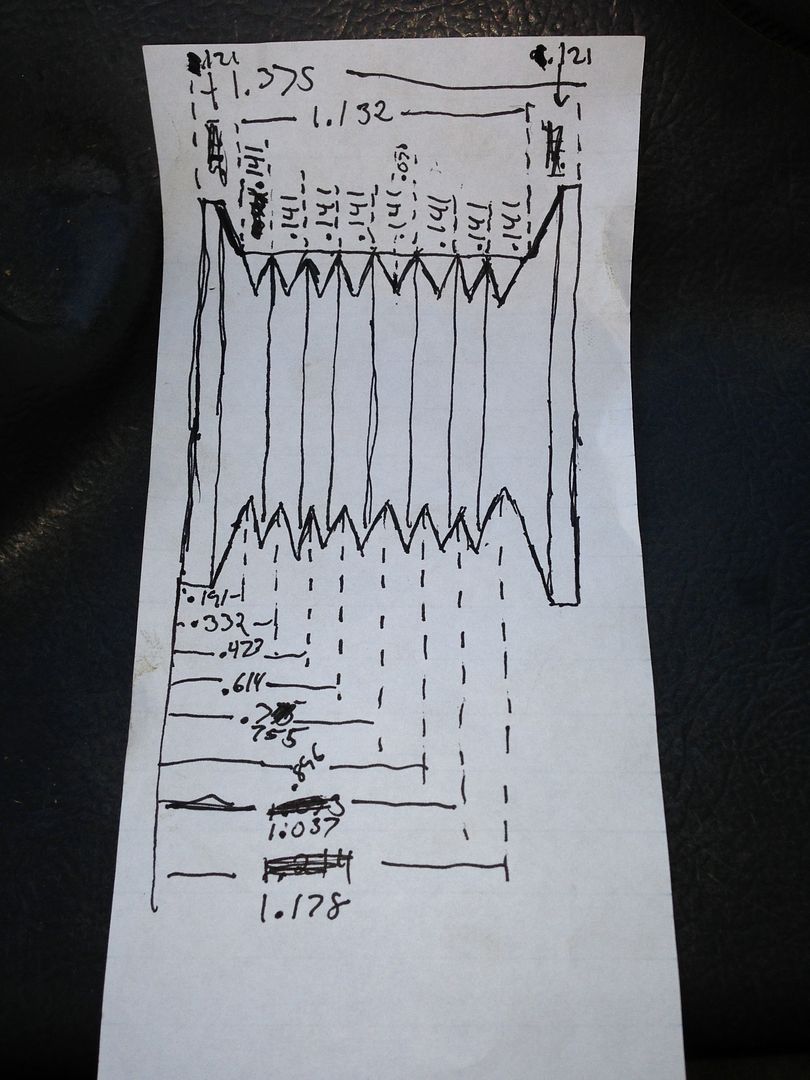
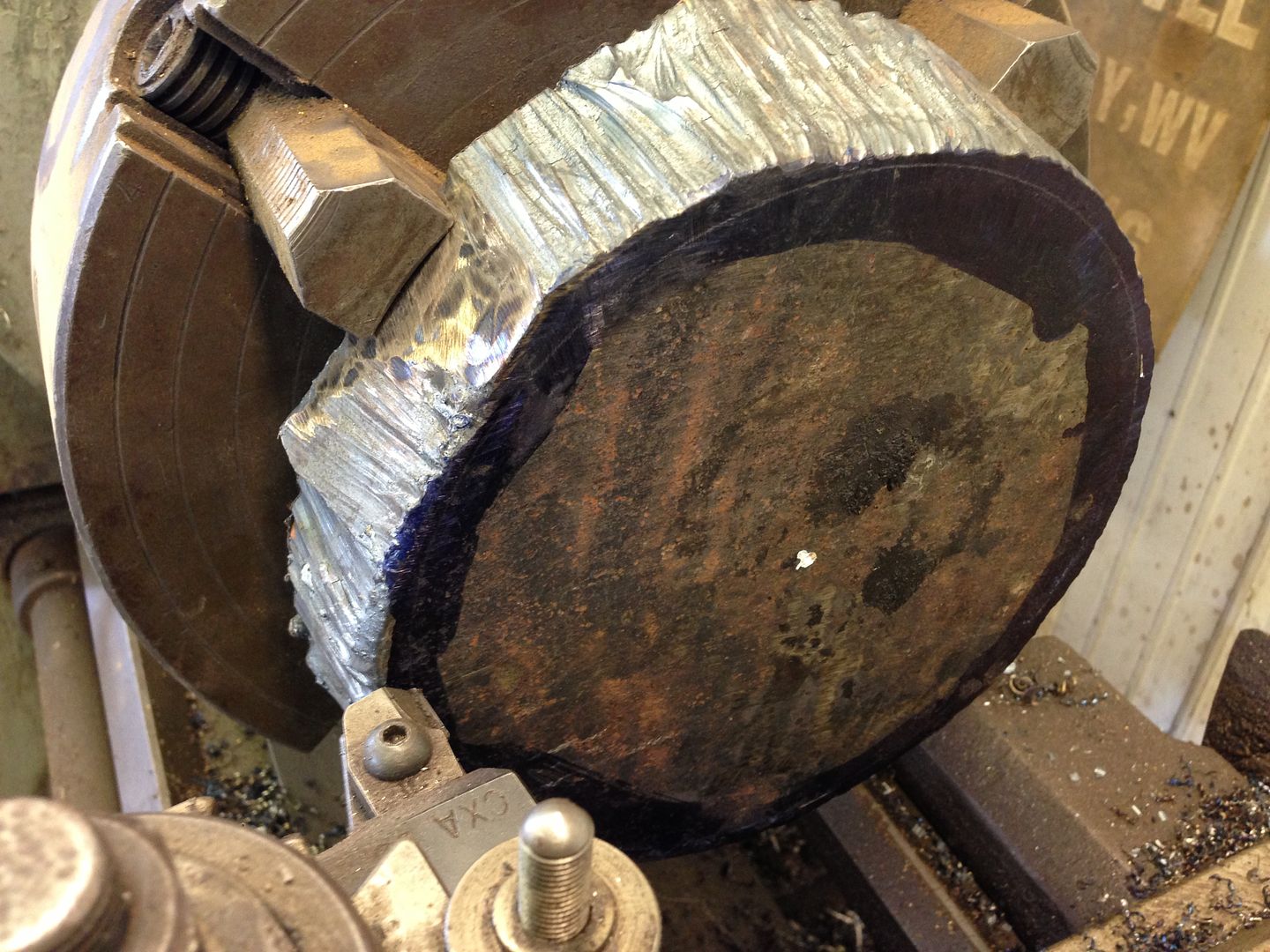
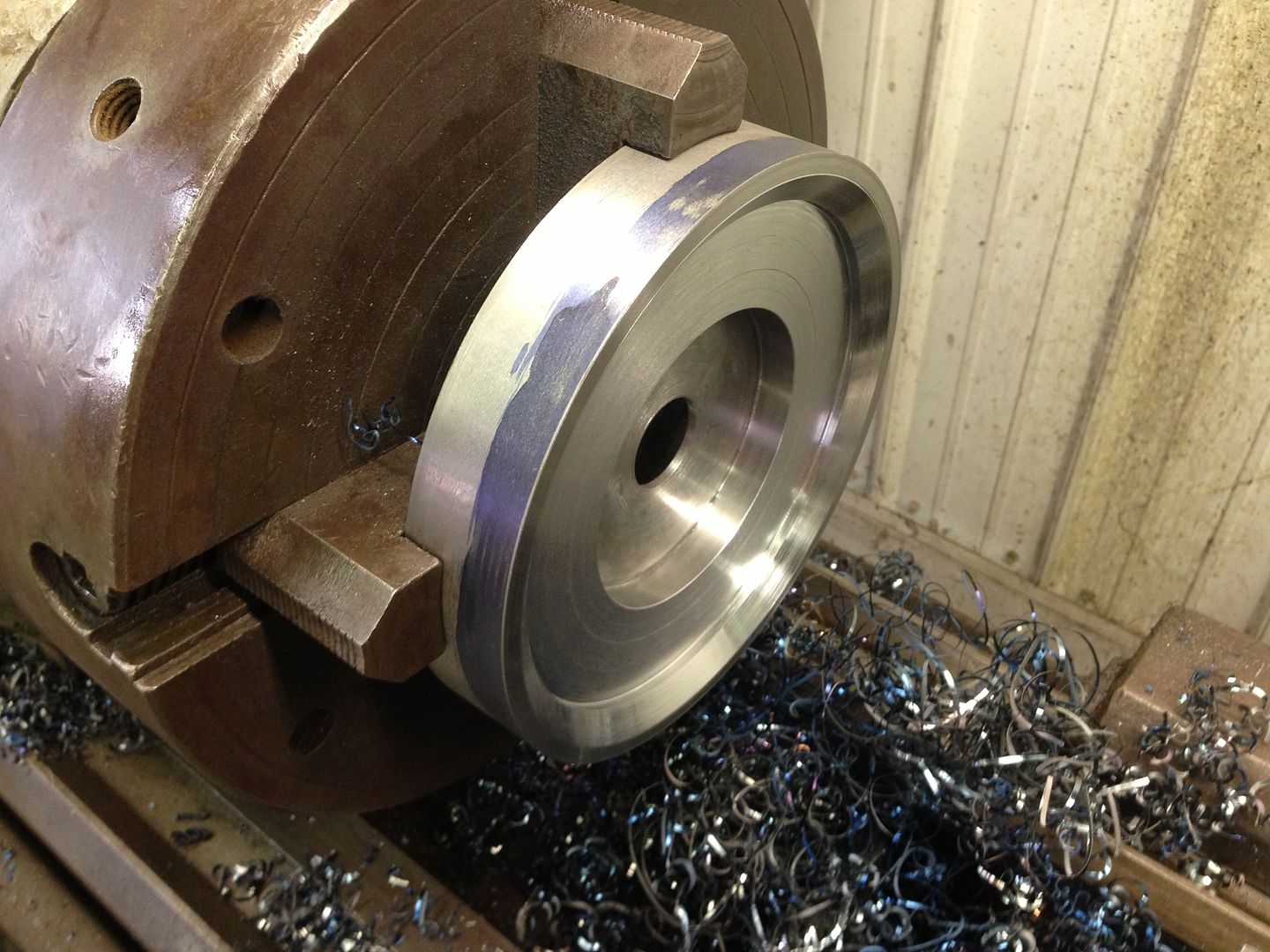
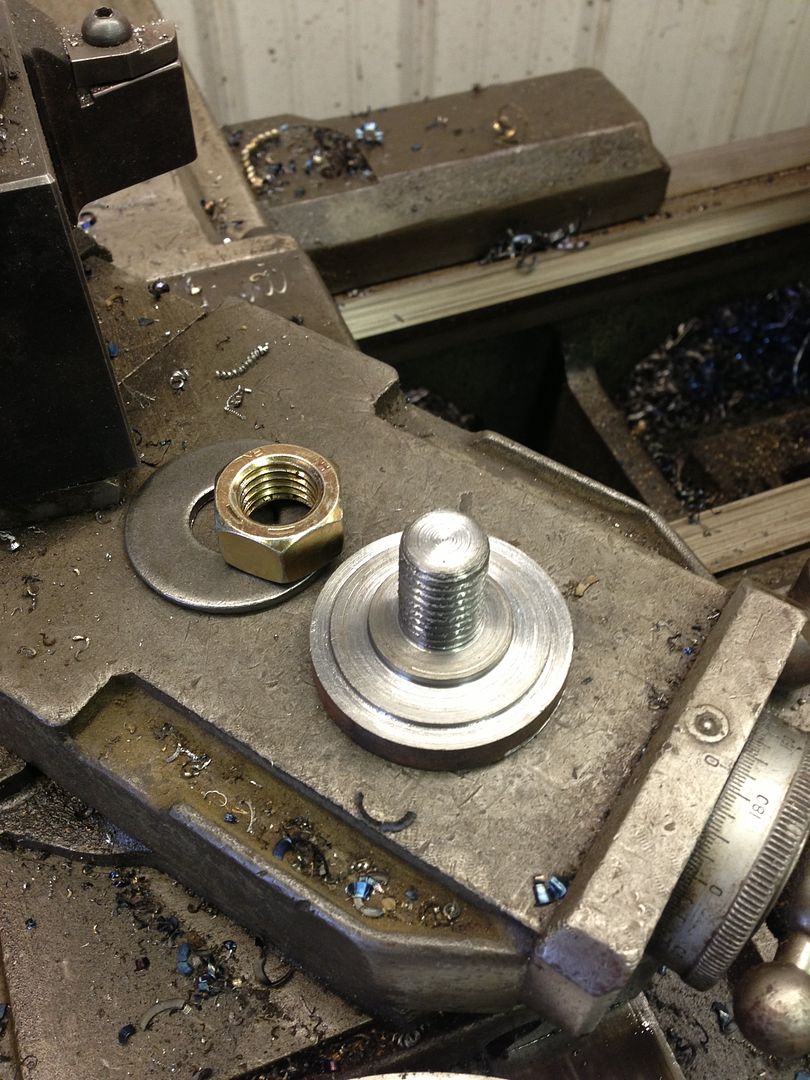
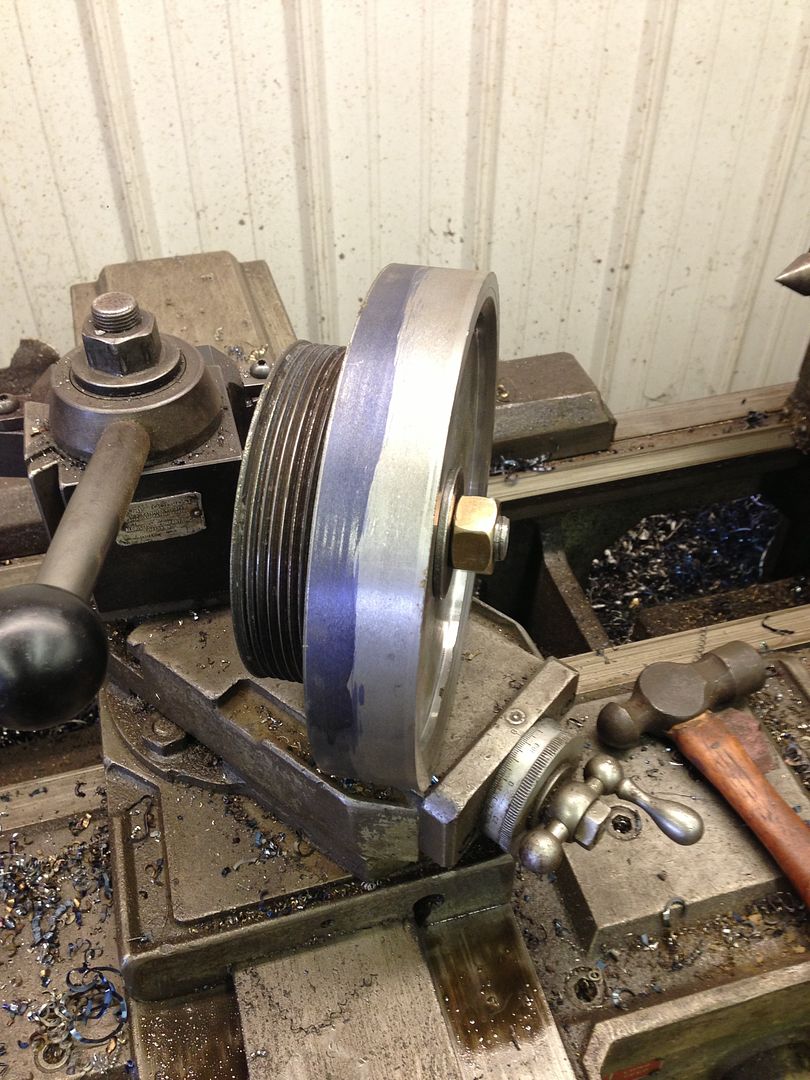
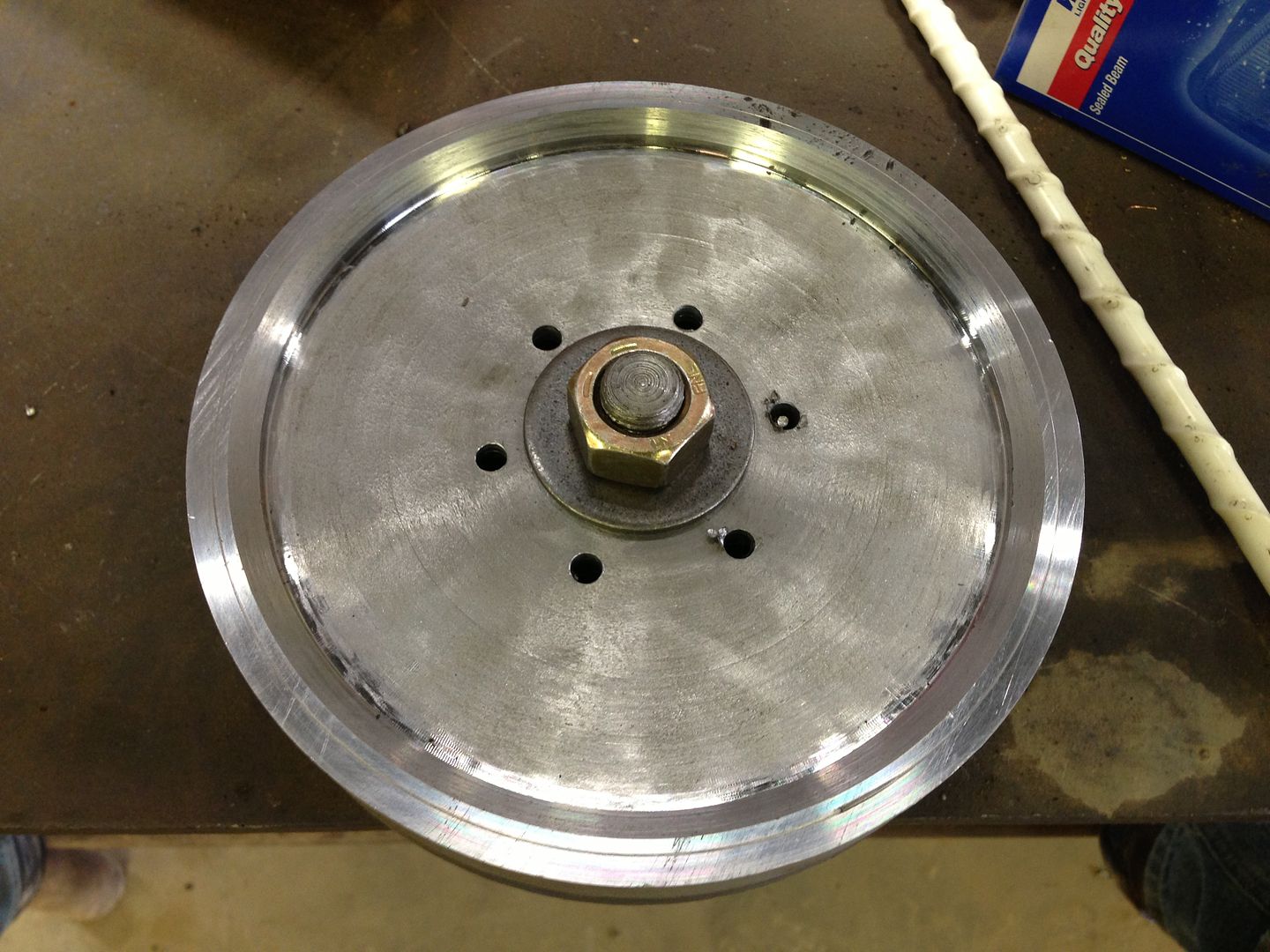
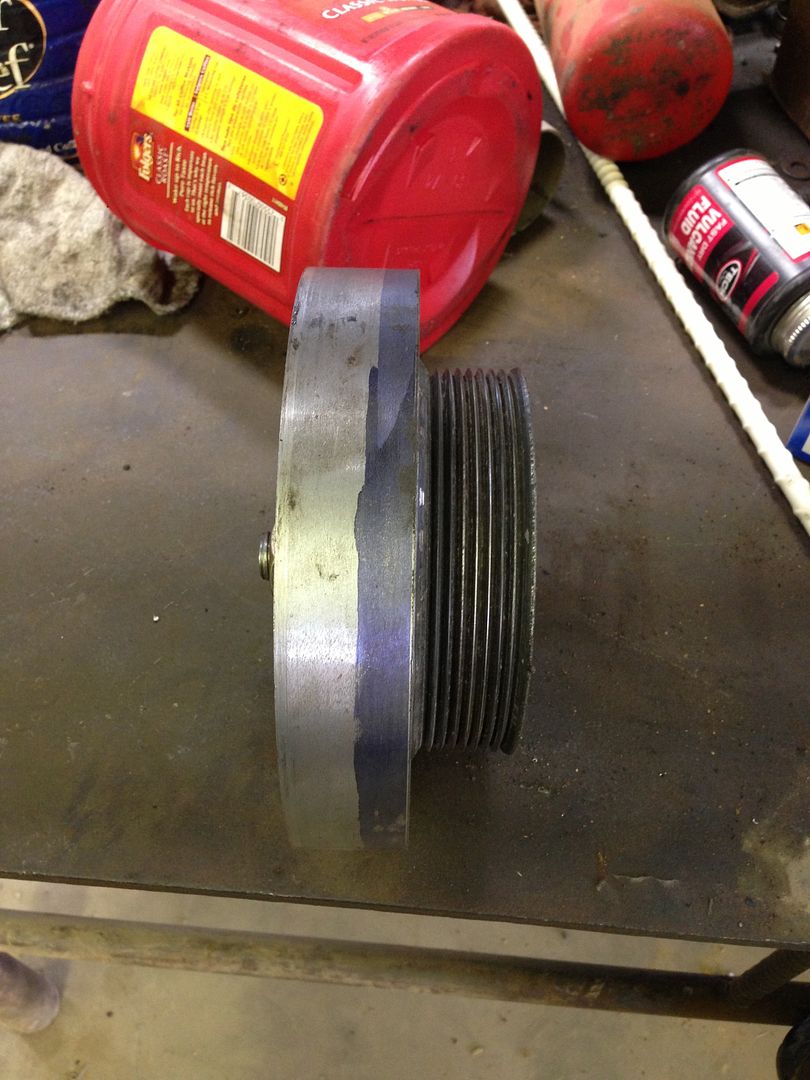
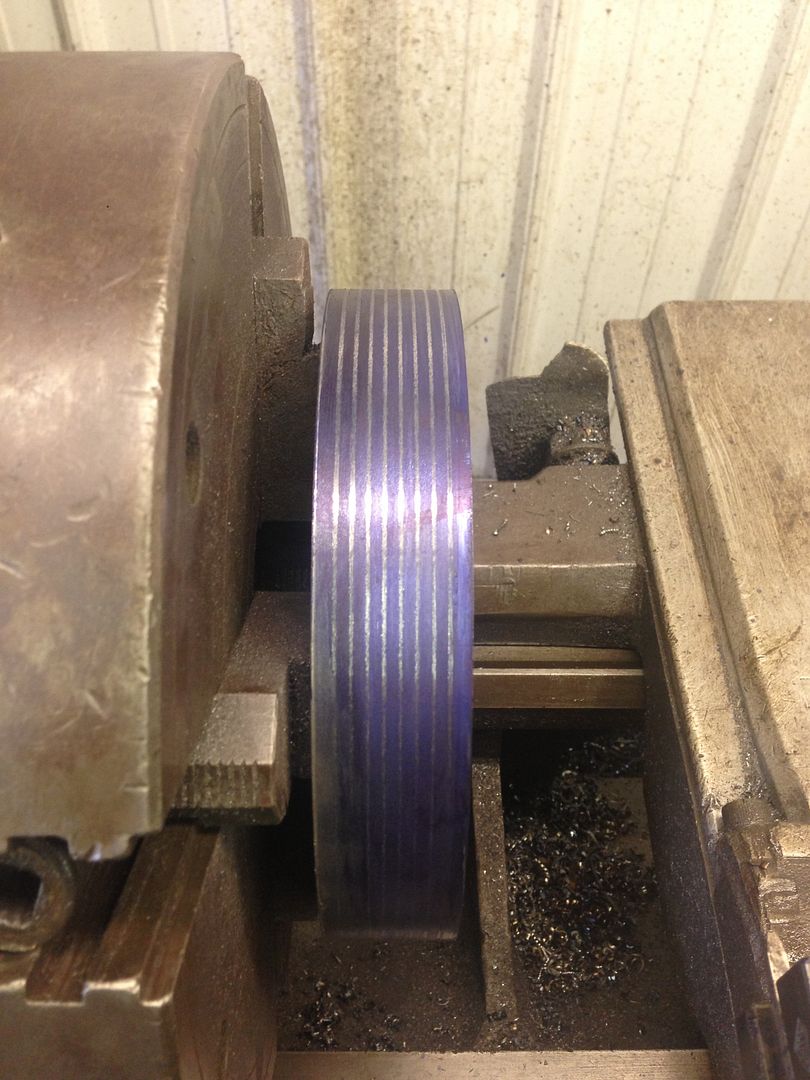