hemijosh426
honey badger dont care
- Joined
- Dec 24, 2009
- Messages
- 57
Finally getting some time to work on a swap I have been planning for awhile. The 1947 Dodge was originally a WD-21 1 ton from NY state roads. Surprisingly all of the sheet metal was in great shape, and needed minimal work to get into paint. I bought the truck completely stripped to bare metal, and due to life getting in the way it took awhile to make it into the paint stage. The paint is a cheap single stage jet black, I just wanted to get a couple coats of primer and a layer of paint on the truck to protect it from the elements. I plan to re-spray it with base/clear one day after I am finished the swap. I figured that I would be scratching it up while working on the project, and it wasnt worth making a perfect paint job right off the bat.
I am doing a full frame swap from a 1993 Dodge D250 2wd Cummins with a 47RH lockup automatic. This way I will have newer steering, suspension, and brakes. I also plan on possibly utilizing the factory 93 gauges in the dash of the 47. I put the 47RH in the 93 a few years back.
For pedals and steering wheel I hope to use the 93 Dodge pieces, cut them directly out of the firewall of the 93 and makes some brackets to run them in the 47. This may change, but thats the initial plan lol.
Heres a pic of the truck the day I picked it up
After a few coats of primer
And finally into paint
And so the work begins for taking the 93 and 47 apart
This didnt work so well. The cab fell off the engine crane, but luckily I had safety straps that caught it. I actually ended up moving the cab to the 93 frame with help from 4 friends. Alot easier than playing games with the engine crane again.
Finally the cab just sitting in place on the 93
It appears I will have to move the engine back about a foot from where it sits now, so that I can fit a radiator and an intercooler. I will also have to modify the 2wd front suspension, because the fenders of the 47 do not go far enough forward to go past the Srut arms that hold the lower control arm in place.
I also have an old school Holmes wrecker boom to go on the frame of the truck. I will be mounting the wrecker boom inside of the original bed.
I am also planning on flipping the turbo upside down with a 3rd gen Dodge Cummins manifold upside down, and then running a hood stack... No clearance at the firewall after I move the motor back.
The current VE 12v in the 93 has 7x.010 injectors and a BD Super B 62 turbo with a 3200 spring in the pump and the fuel screw all the way out. Should make this little 47 pretty quick.
More pics to follow!
I am doing a full frame swap from a 1993 Dodge D250 2wd Cummins with a 47RH lockup automatic. This way I will have newer steering, suspension, and brakes. I also plan on possibly utilizing the factory 93 gauges in the dash of the 47. I put the 47RH in the 93 a few years back.
For pedals and steering wheel I hope to use the 93 Dodge pieces, cut them directly out of the firewall of the 93 and makes some brackets to run them in the 47. This may change, but thats the initial plan lol.
Heres a pic of the truck the day I picked it up

After a few coats of primer
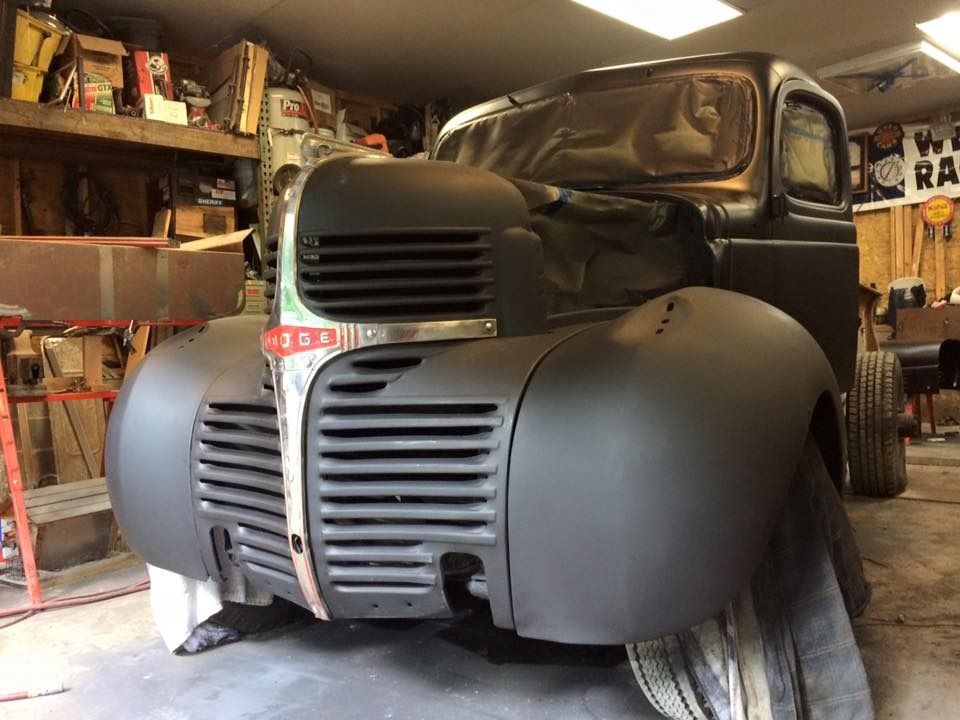
And finally into paint
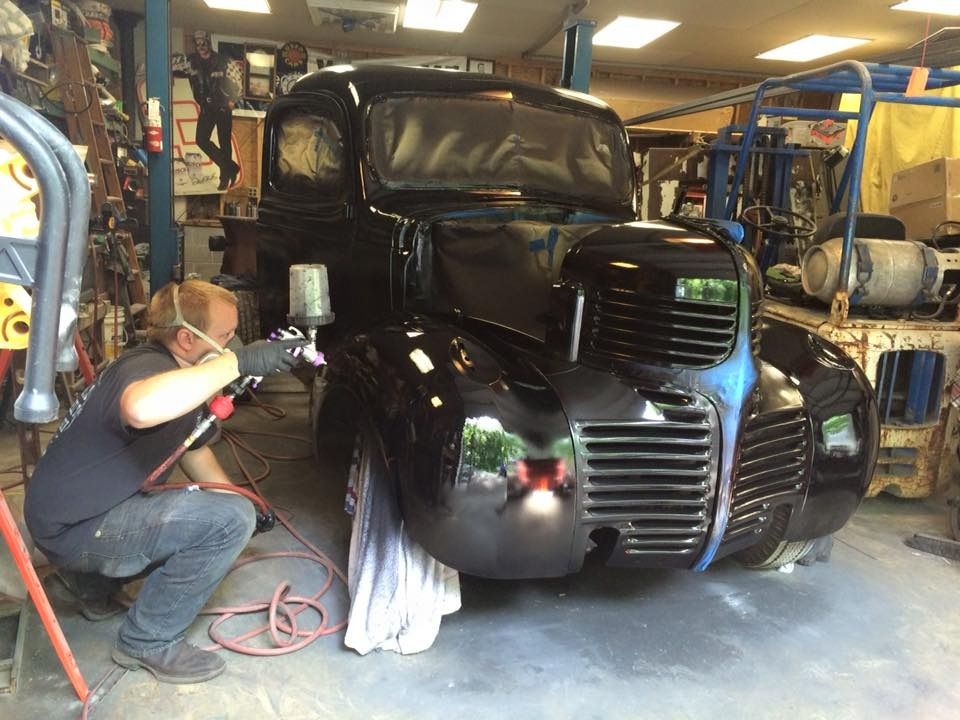
And so the work begins for taking the 93 and 47 apart
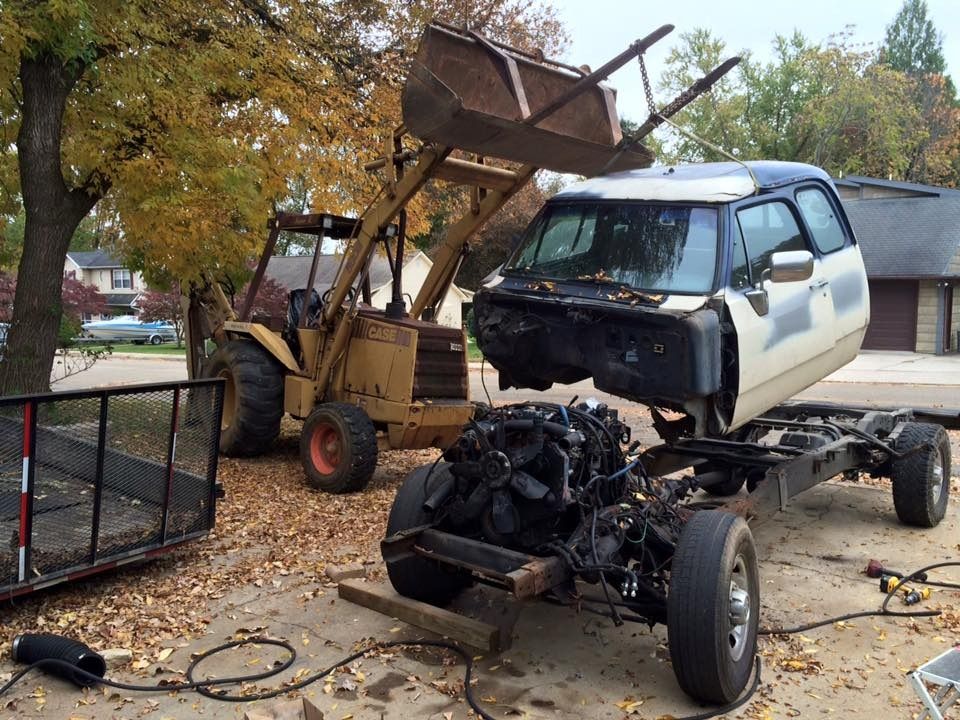
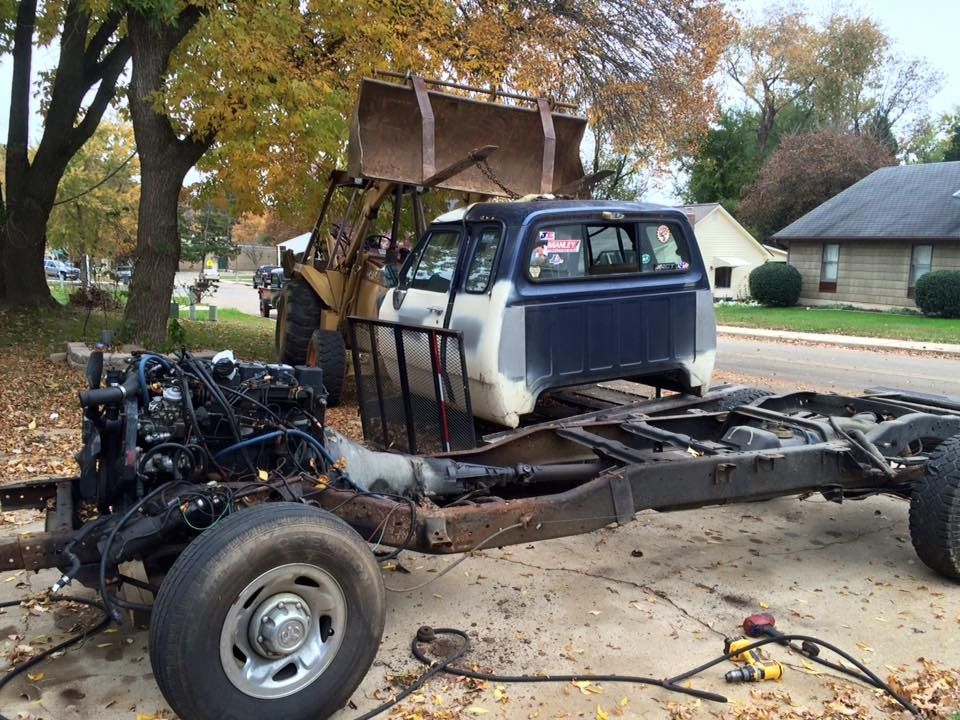
This didnt work so well. The cab fell off the engine crane, but luckily I had safety straps that caught it. I actually ended up moving the cab to the 93 frame with help from 4 friends. Alot easier than playing games with the engine crane again.
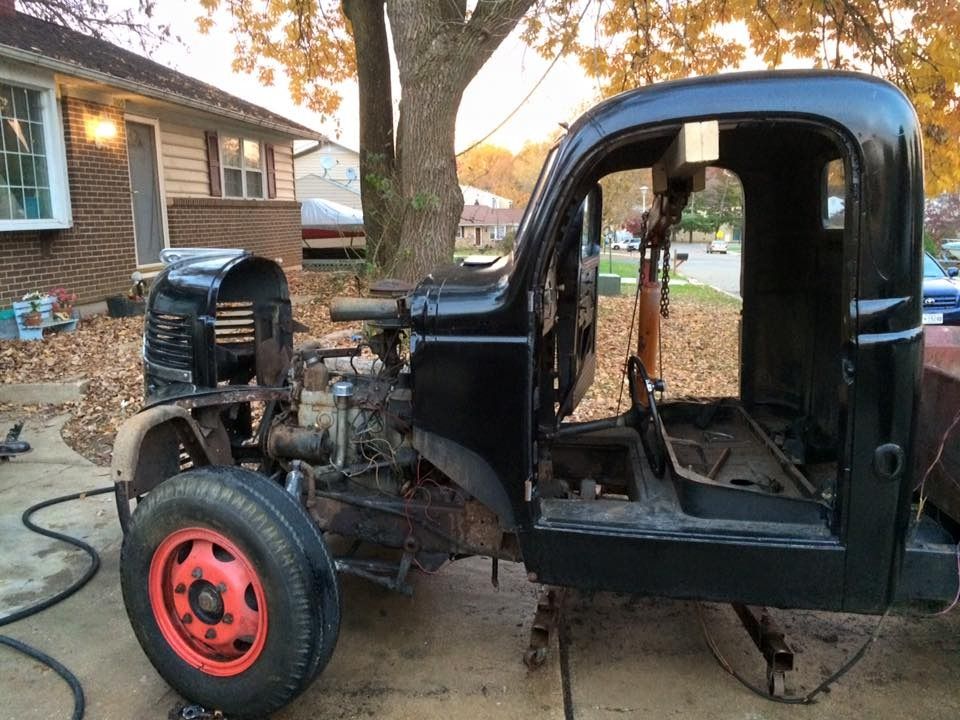
Finally the cab just sitting in place on the 93
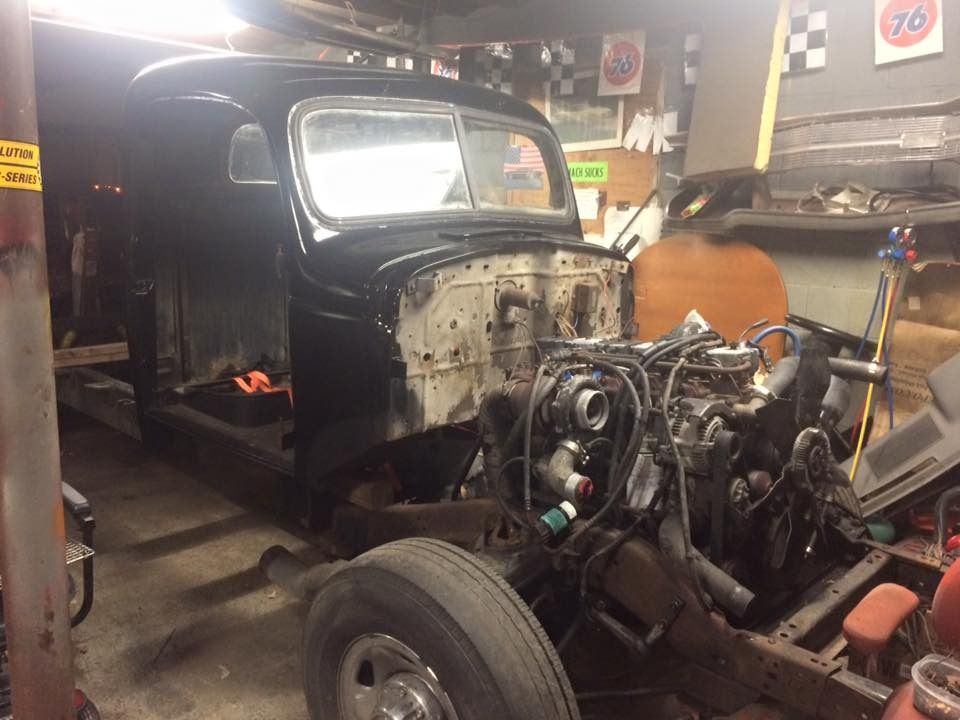
It appears I will have to move the engine back about a foot from where it sits now, so that I can fit a radiator and an intercooler. I will also have to modify the 2wd front suspension, because the fenders of the 47 do not go far enough forward to go past the Srut arms that hold the lower control arm in place.
I also have an old school Holmes wrecker boom to go on the frame of the truck. I will be mounting the wrecker boom inside of the original bed.
I am also planning on flipping the turbo upside down with a 3rd gen Dodge Cummins manifold upside down, and then running a hood stack... No clearance at the firewall after I move the motor back.
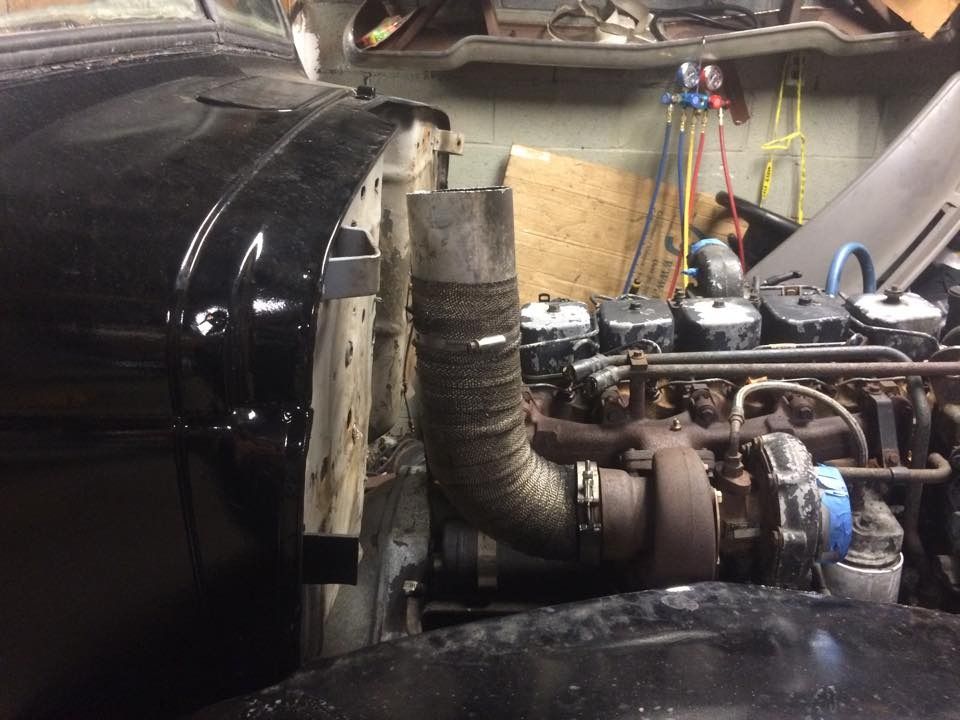
The current VE 12v in the 93 has 7x.010 injectors and a BD Super B 62 turbo with a 3200 spring in the pump and the fuel screw all the way out. Should make this little 47 pretty quick.
More pics to follow!