First post here guys. I've been gathering parts and info on building a little different setup than a pull truck rear dana 80 but rather a rear steer 40 spline with dodge kingpin dana 60 outters.
I've found some good info in here and I thought I'd share my plans and ideas on this build.
Started with a '04, F450, 37 spline D80 and a Dodge( not sure year) kingpin axle.
Paid only $200 for the d80 and $600 for the d60.
After reasearch I found the 37 spline d80 from a f450 should have massive 11/16" tubes! After cutting off spindles to desired length to make a 73" wms I found this was true
Chopped up the d60 from the C's out..
Now with this setup the biggest concern on putting them together is the 4" tube sliding into a 3 1/4" inner ID of the dana 60 C.
So without boring the crap out of the C, I decided I'm going to bolt the outter d60 with a 3/4" flange with 1/2" bolts with the ability to clock pinion angle and pull ends for easy repair or maintenance
Like this
I have a shop that will burn out the 4 rings with 2 having a 4" ID and 2 with 3.25" ID but same bolt pattern.
My inner axle shafts I purchased CTM 300m joints as well as paid a half deposit on CTM 300m shafts.
Here's where I decided I will upgrade to bigger 1.75" 40 spline shafts after realizing all the same cost to go bigger as he starts with a 1.75 blank.
Jack at CTM took some measurements on a set of d80 ,37 spline spiders he has kicking around and found the have enough meat to be broached to 40.
I mailed out my 37 spline spiders yesterday to be broached to 40 and I just plan to weld a spool for now with no steering concerns as it will be powered by a PSC 2.75x8 double ended ram anyway.
I've purchased 5:13 gears as well.
CTM will also be making me a set of d60 hub drive flanges out of 300m.
I've found some good info in here and I thought I'd share my plans and ideas on this build.
Started with a '04, F450, 37 spline D80 and a Dodge( not sure year) kingpin axle.
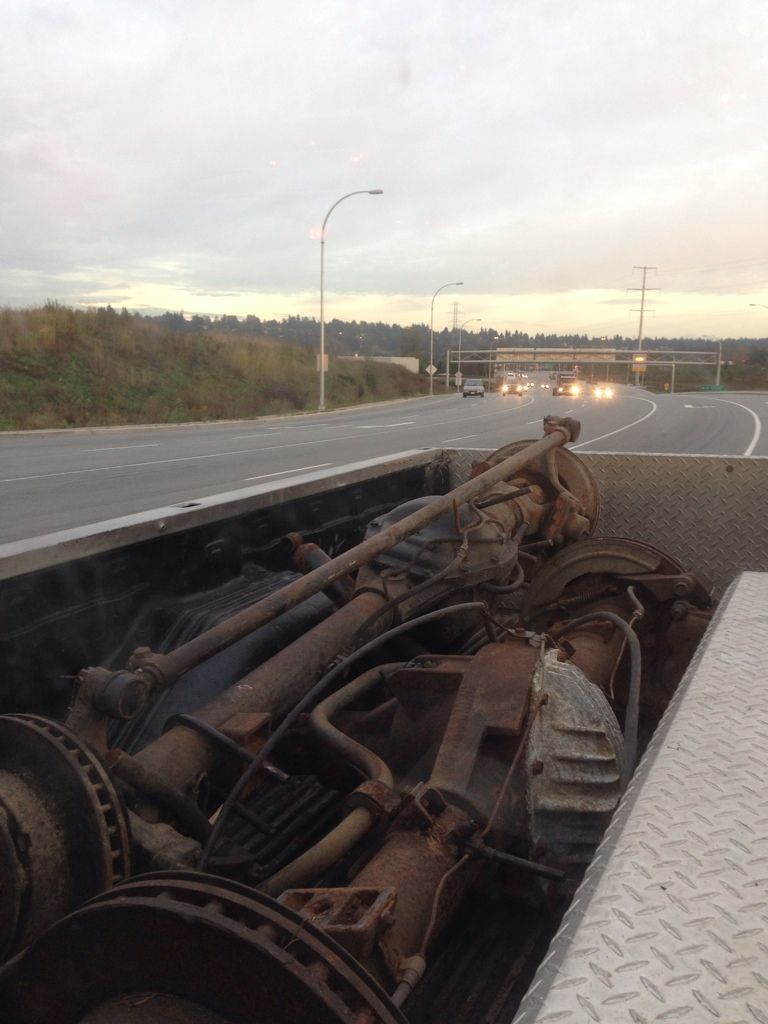
Paid only $200 for the d80 and $600 for the d60.
After reasearch I found the 37 spline d80 from a f450 should have massive 11/16" tubes! After cutting off spindles to desired length to make a 73" wms I found this was true
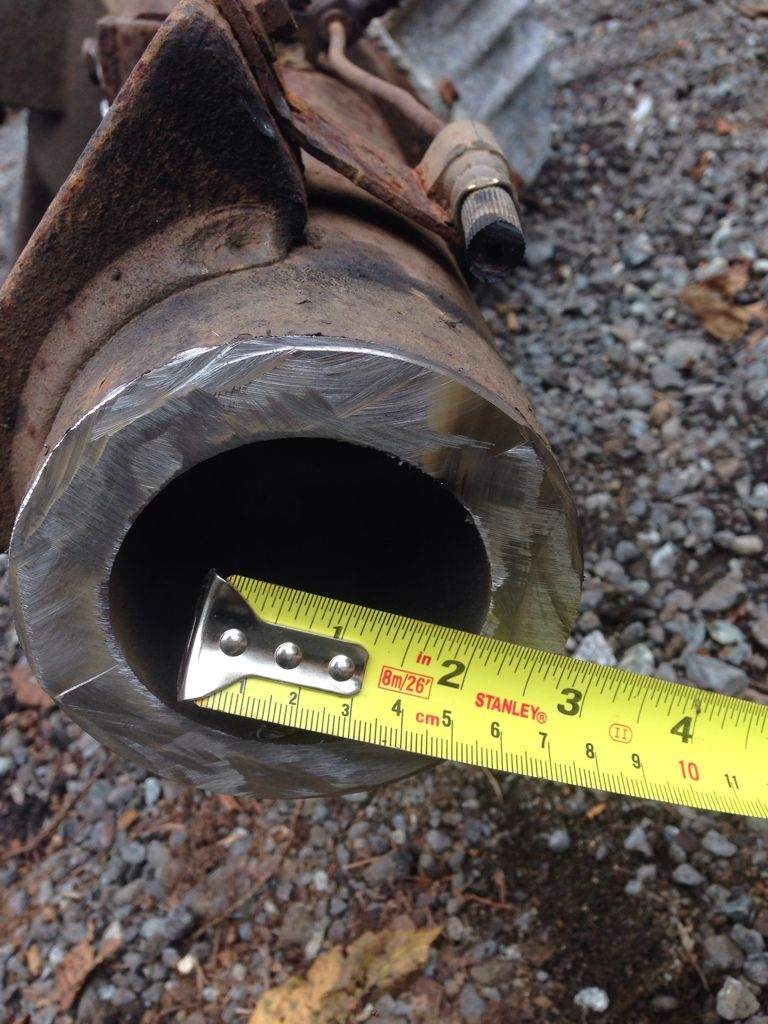
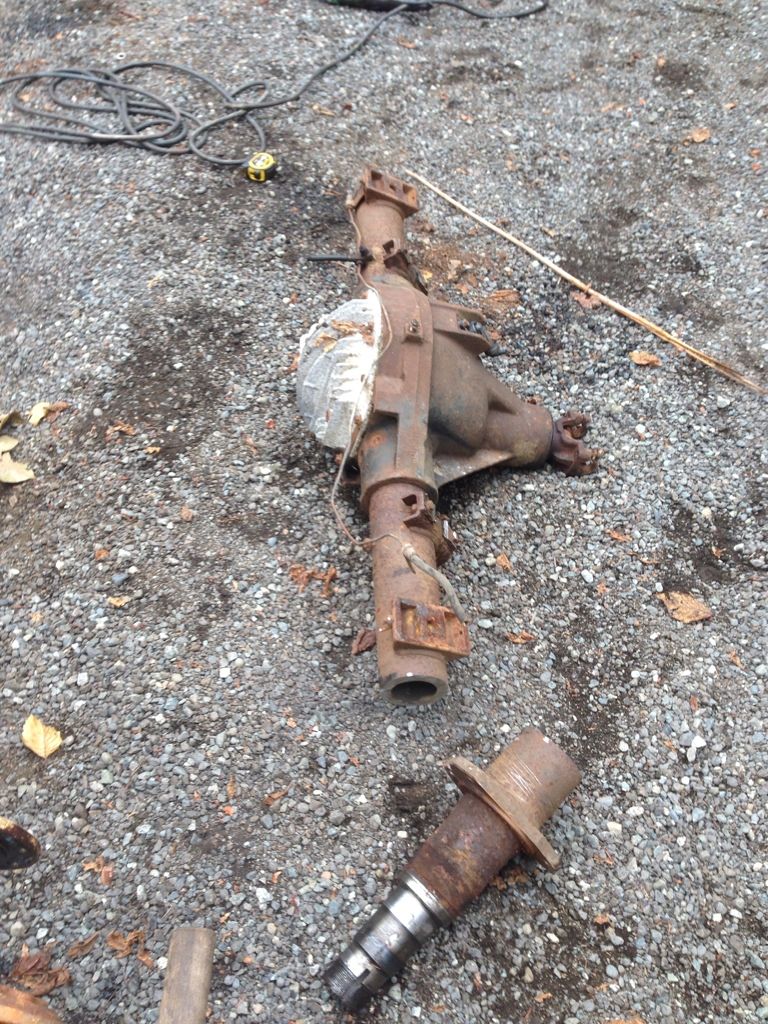
Chopped up the d60 from the C's out..
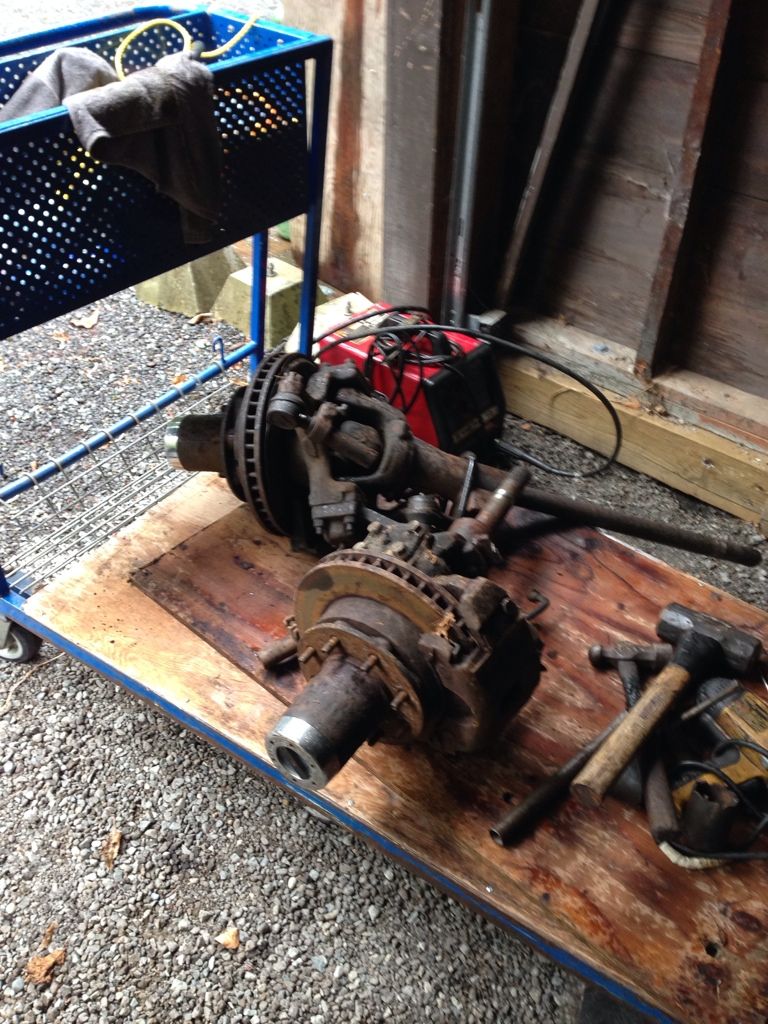
Now with this setup the biggest concern on putting them together is the 4" tube sliding into a 3 1/4" inner ID of the dana 60 C.
So without boring the crap out of the C, I decided I'm going to bolt the outter d60 with a 3/4" flange with 1/2" bolts with the ability to clock pinion angle and pull ends for easy repair or maintenance
Like this
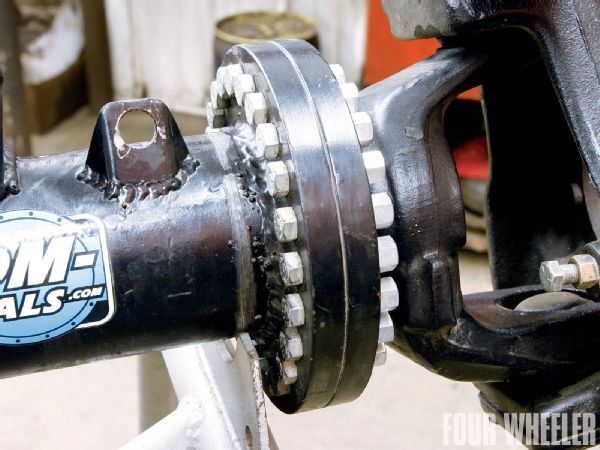
I have a shop that will burn out the 4 rings with 2 having a 4" ID and 2 with 3.25" ID but same bolt pattern.
My inner axle shafts I purchased CTM 300m joints as well as paid a half deposit on CTM 300m shafts.
Here's where I decided I will upgrade to bigger 1.75" 40 spline shafts after realizing all the same cost to go bigger as he starts with a 1.75 blank.
Jack at CTM took some measurements on a set of d80 ,37 spline spiders he has kicking around and found the have enough meat to be broached to 40.
I mailed out my 37 spline spiders yesterday to be broached to 40 and I just plan to weld a spool for now with no steering concerns as it will be powered by a PSC 2.75x8 double ended ram anyway.
I've purchased 5:13 gears as well.
CTM will also be making me a set of d60 hub drive flanges out of 300m.
Last edited: